Lean Manufacturing
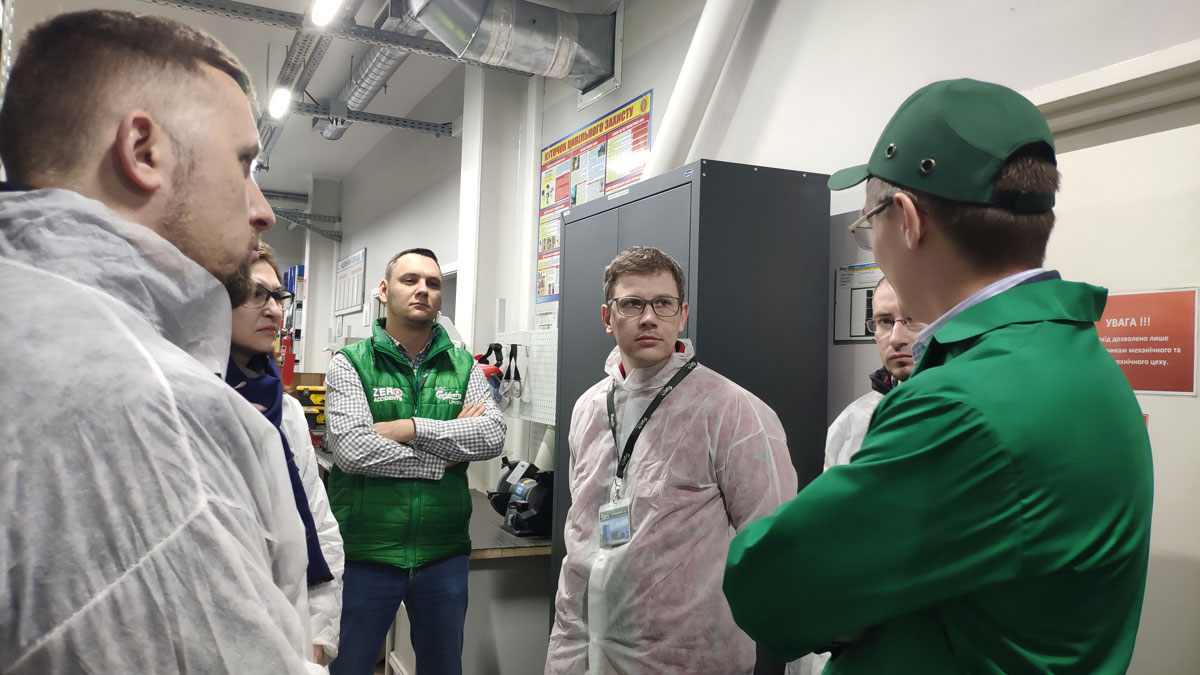
Our goal is to turn Extreme LTD into a “lean company”. We perceive this as a far-sighted approach to the development of the enterprise and a respectful attitude to organizational, production and financial resources, to everything that the company does. We systematically reduce all unproductive costs and create new resources that we can direct to development.
In the process of implementing the two main elements of our strategy, serving the client and strengthening the economic and financial condition, the principles of lean manufactoring, which we follow, provide two important advantages: reducing production time and increasing its efficiency.
Employees of Extreme LTD have received training at the LEAN INSTITUTE UKRAINE and are now putting the acquired knowledge into practice.
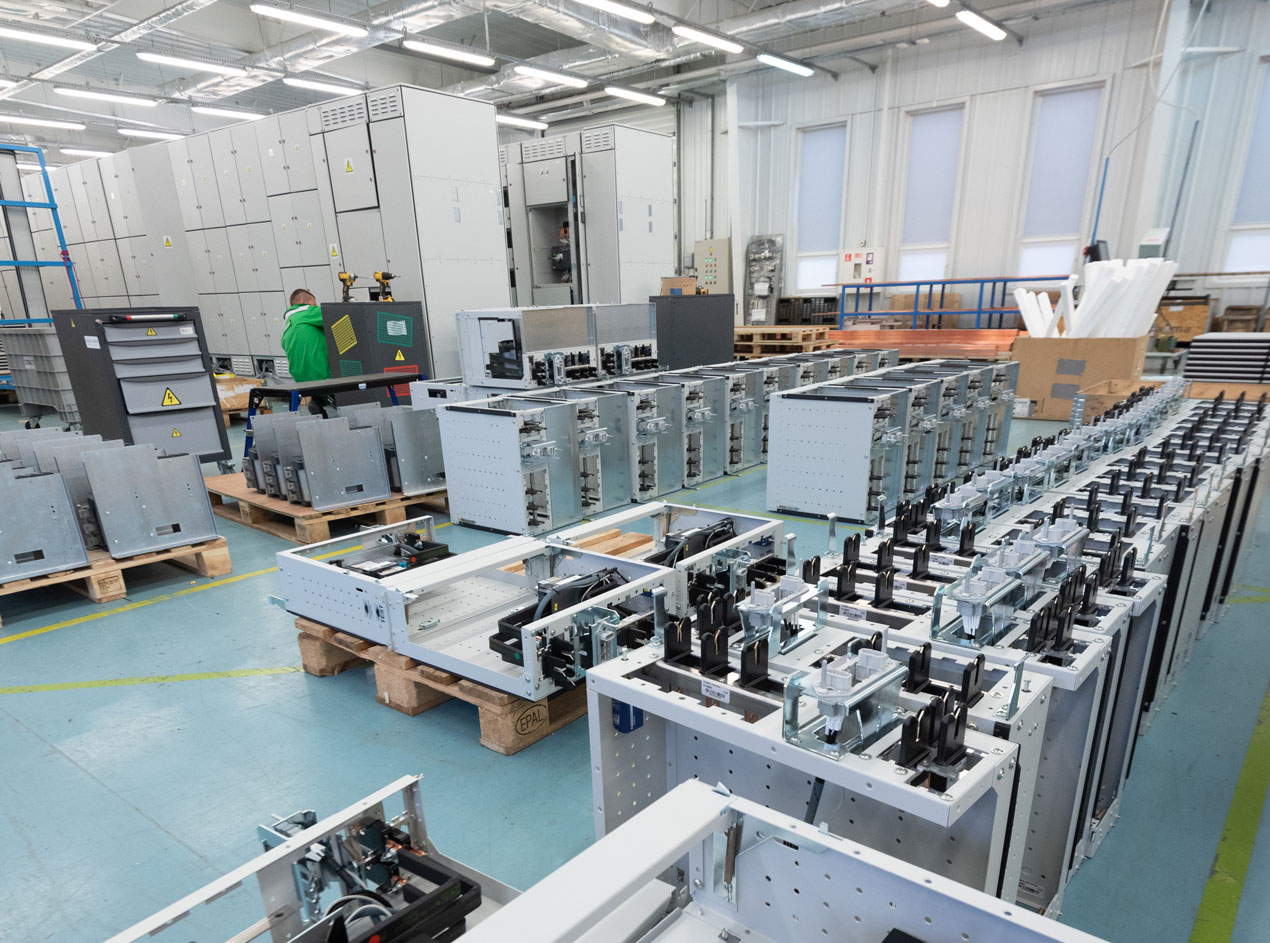
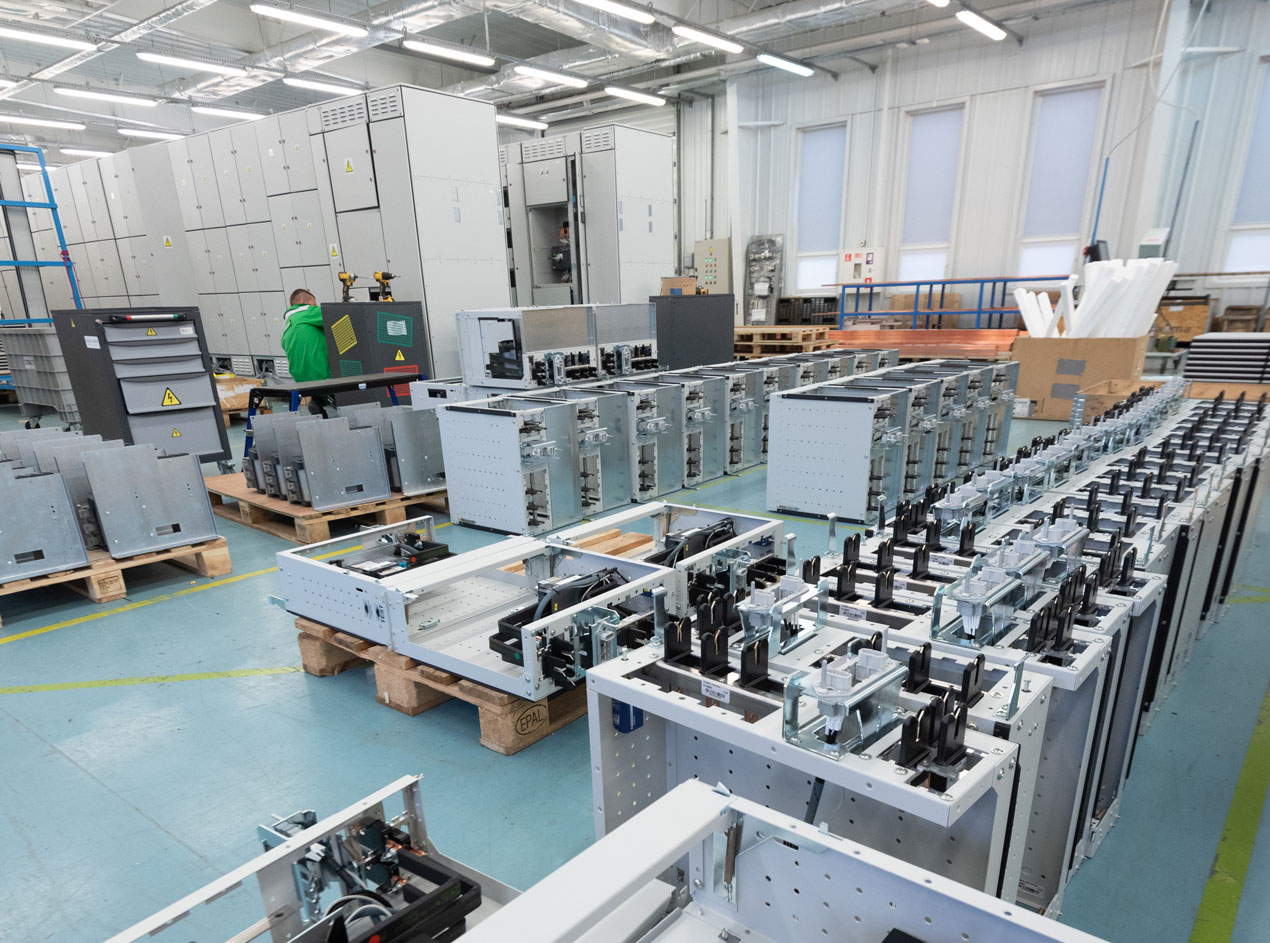
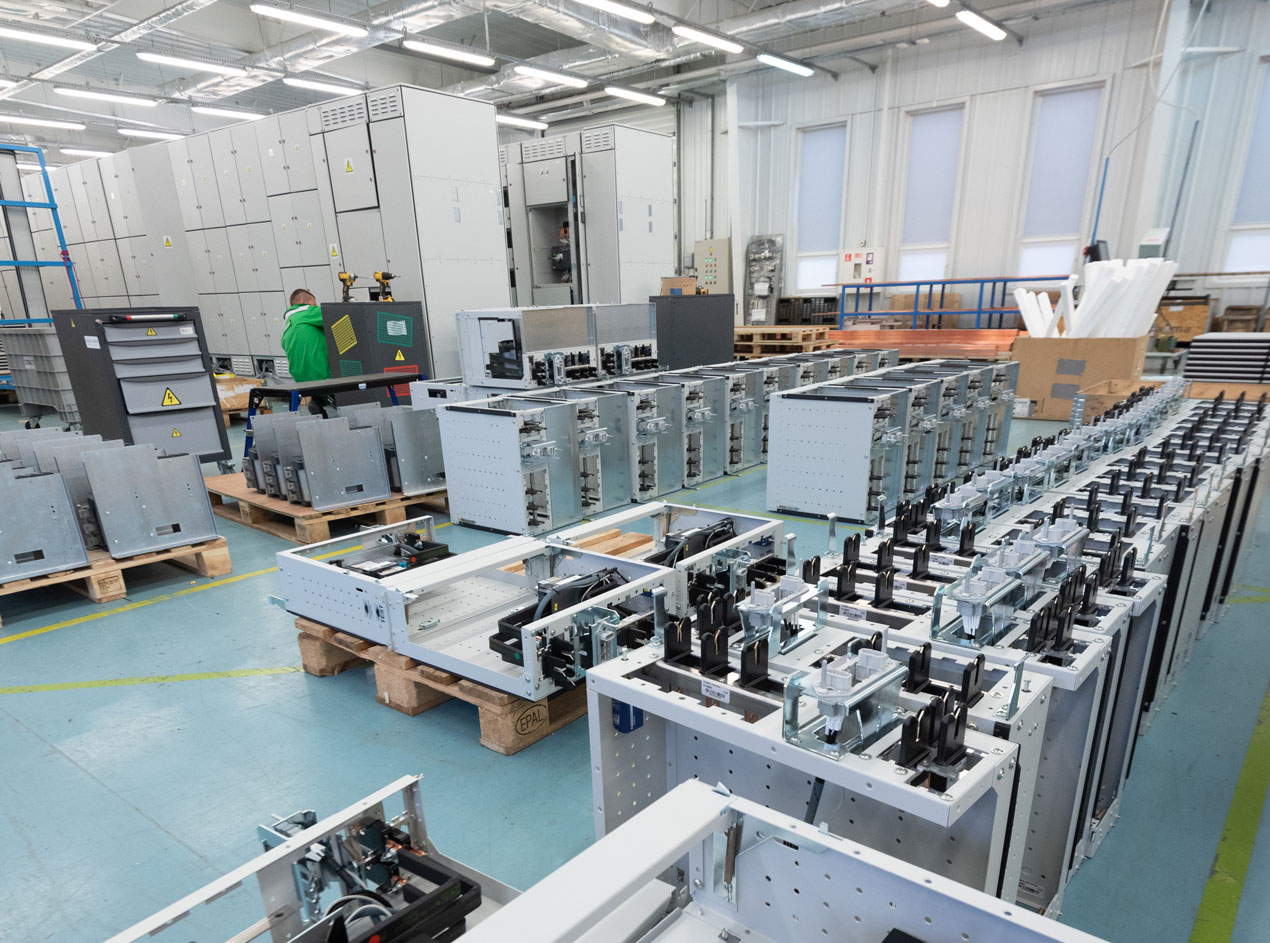
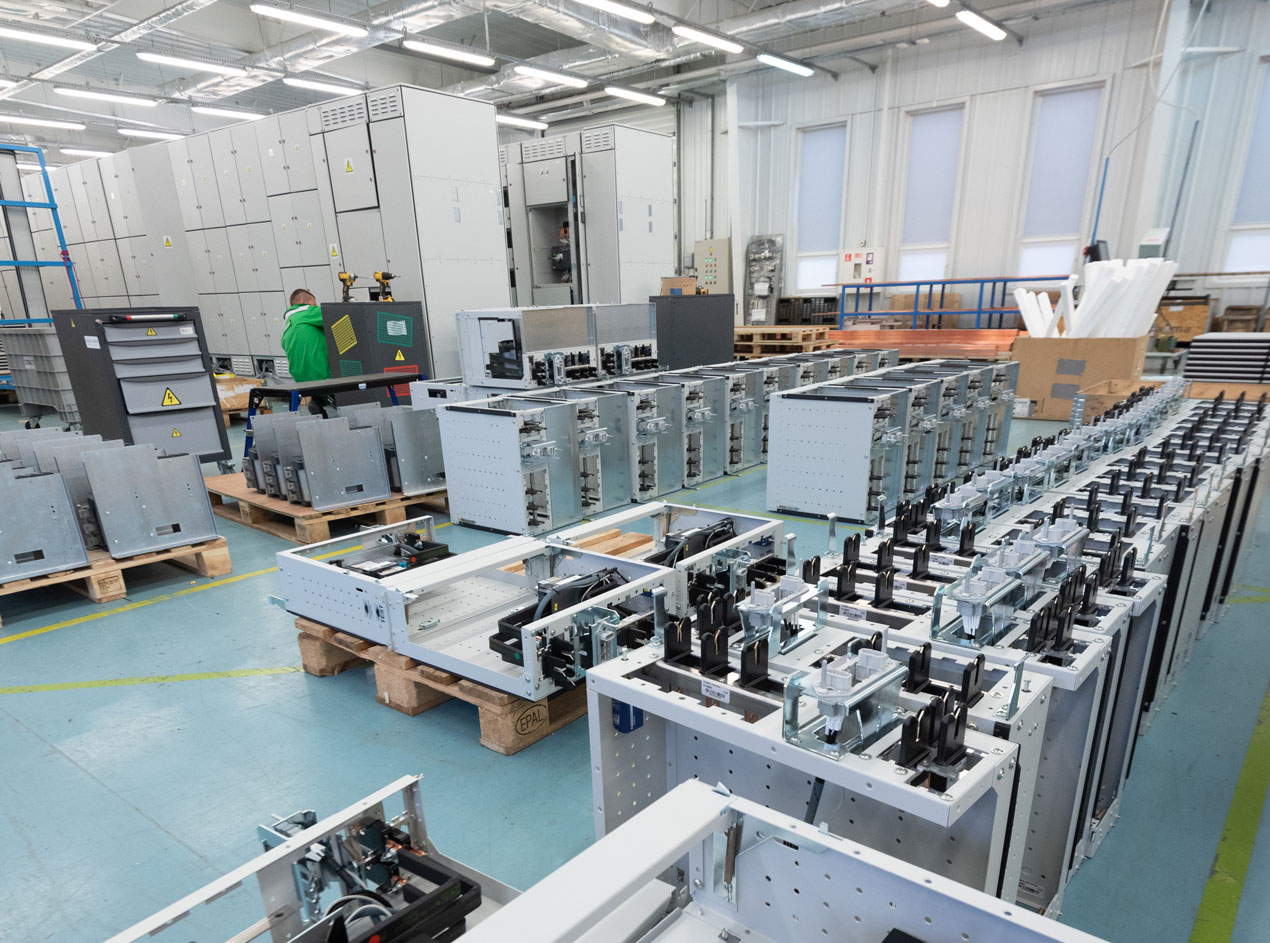
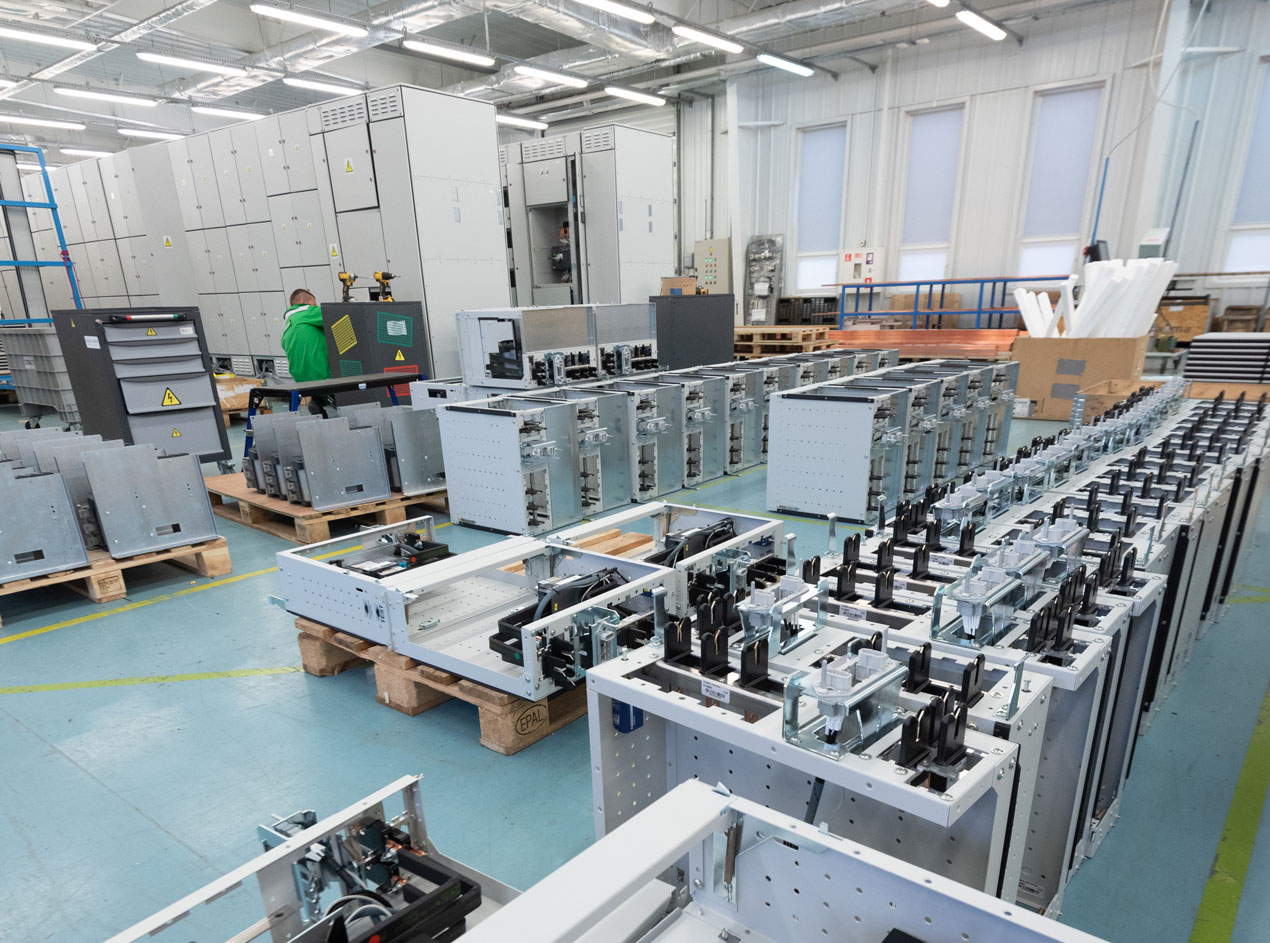
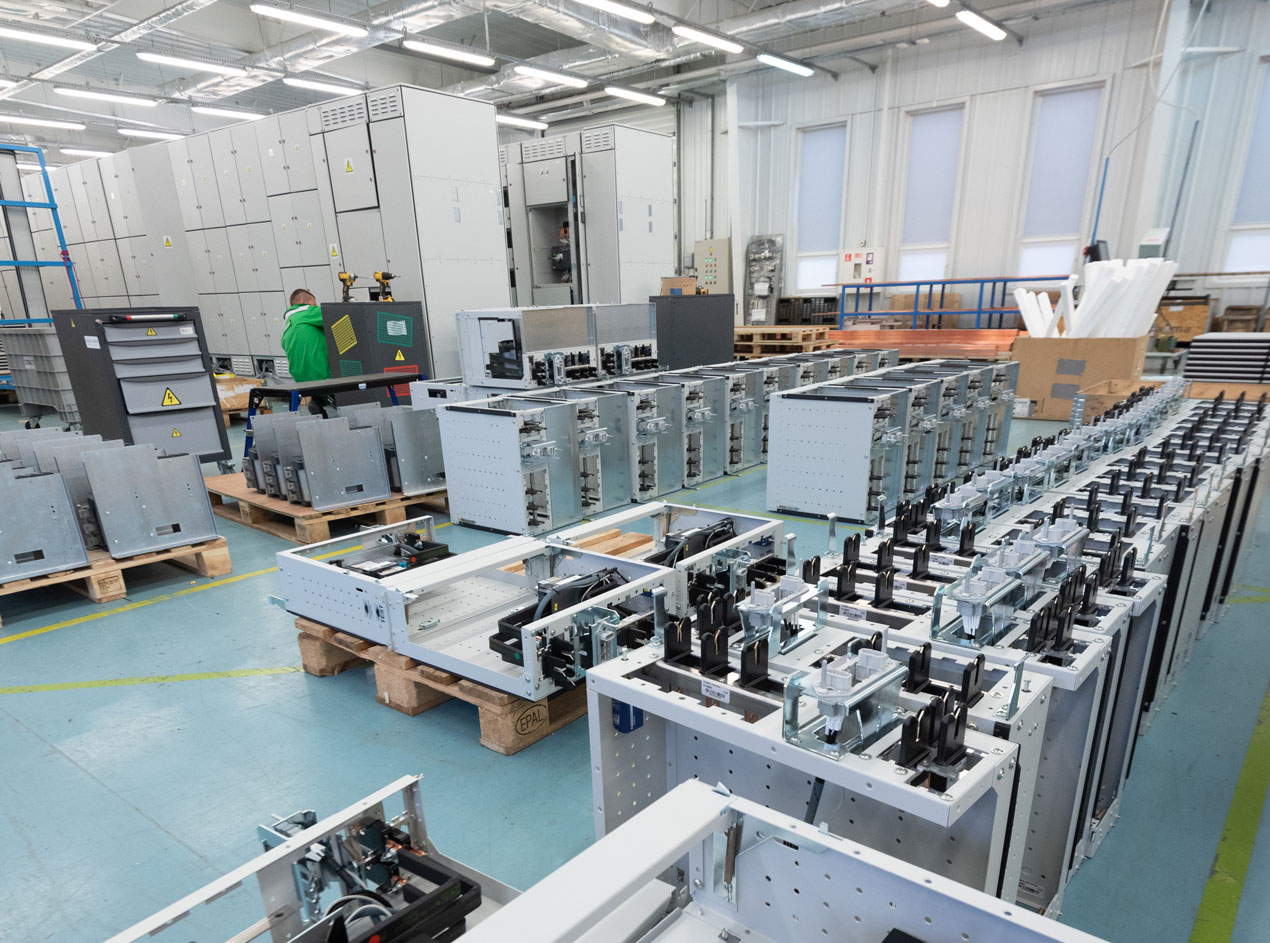
SEIRI (purpose: selection of unnecessary items) – the work begins with the selection and arrangement of unnecessary tools, procedures and items that are not needed to perform specific tasks of the company.
SEITON (goal: better organization of work and systematic activity) is the organization of all necessary tools, products, documents, vehicles along with indicating their exact location so that they are always easily accessible to employees from different departments. The purpose of this stage is to maintain order, for example, in the warehouse, accounting, and workplaces.
SEISO (maintenance of cleanliness and cleaning) – within the framework of this principle, employees must regularly take care of the common space, removing dirt and any garbage.
SEIKETSU (take care of the cleanliness of the workplace) – this stage focuses on maintaining the cleanliness of workplaces. This helps employees understand that a clean workplace means more efficiency and less time to complete tasks.
SHITSUKE – (goal: self-discipline of employees) – the last principle of the 5S idea is the consistency of employees in applying all the above-mentioned actions so that they become useful habits at work.
Increased concentration of employees – the implementation of lean makes employees more focused on achieving a common goal. They are focused on providing the highest possible value to the customer and therefore become more flexible and work with a greater focus on a specific goal.
Increasing the productivity of the team – clear-cut tasks help to build teamwork and avoid misunderstandings in the team, which contributes to increased productivity, better planning of tasks and has a positive effect on reducing working time.
A more efficient process – each stage of the work of a specific department contributes to the achievement of a certain goal, and the team works more efficiently due to the fact that the goals are more precisely defined.
Efficient production without the risk of unnecessary costs – responding to real customer needs reduces the risk of waste. This approach leads to savings for the company.
Elimination of losses – limitation of unnecessary movement of employees, devices, unnecessary transportation on the territory of the company.
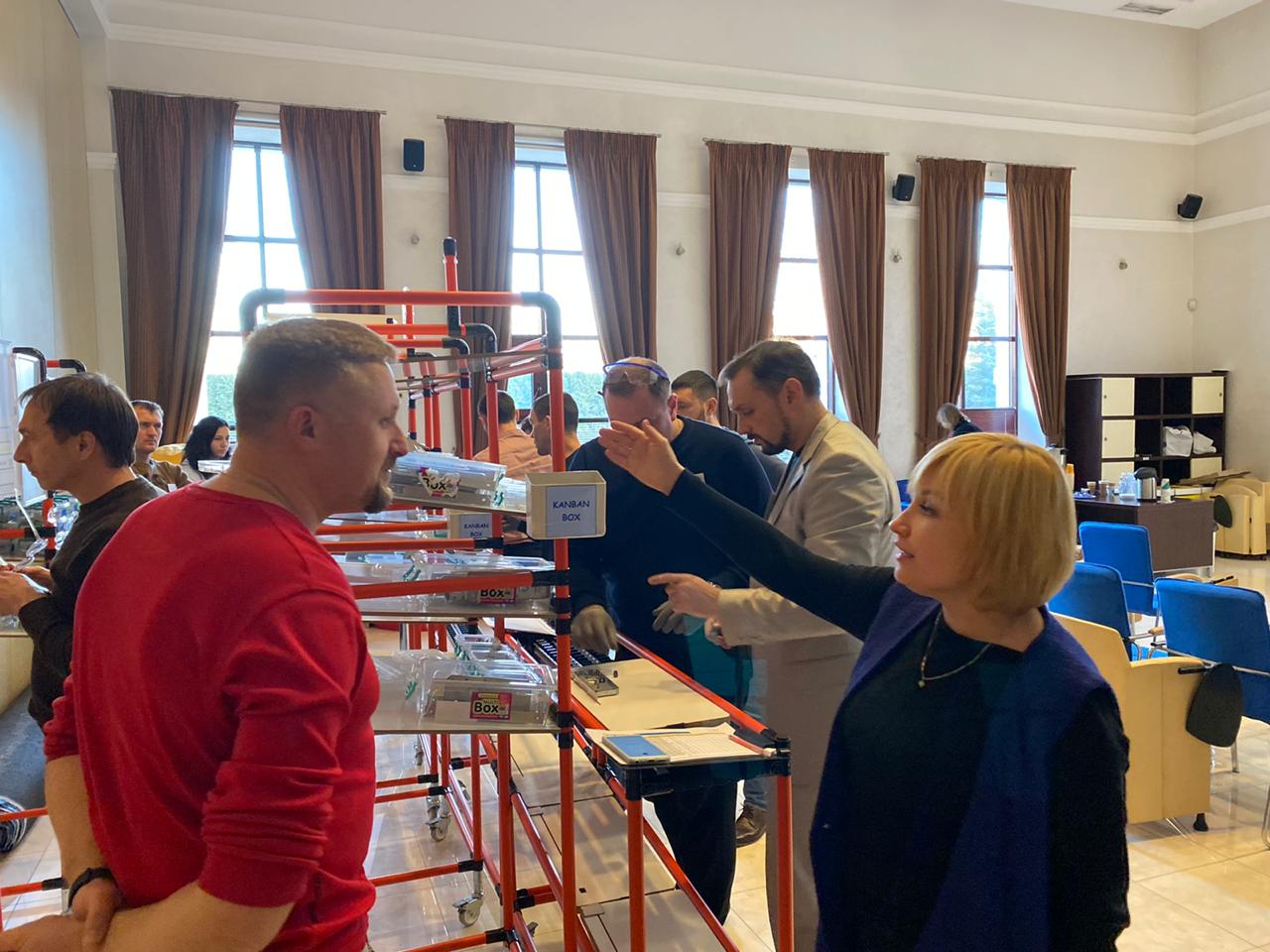
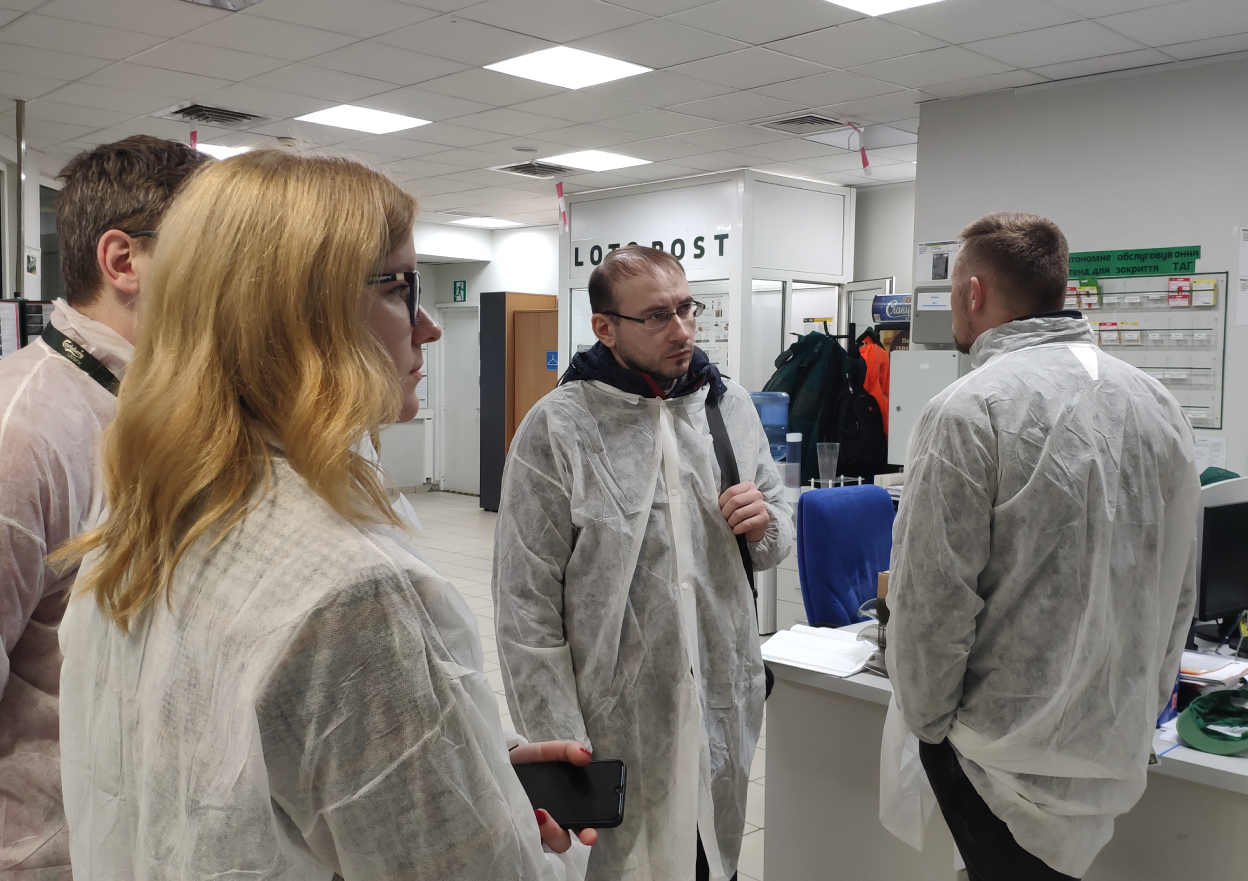
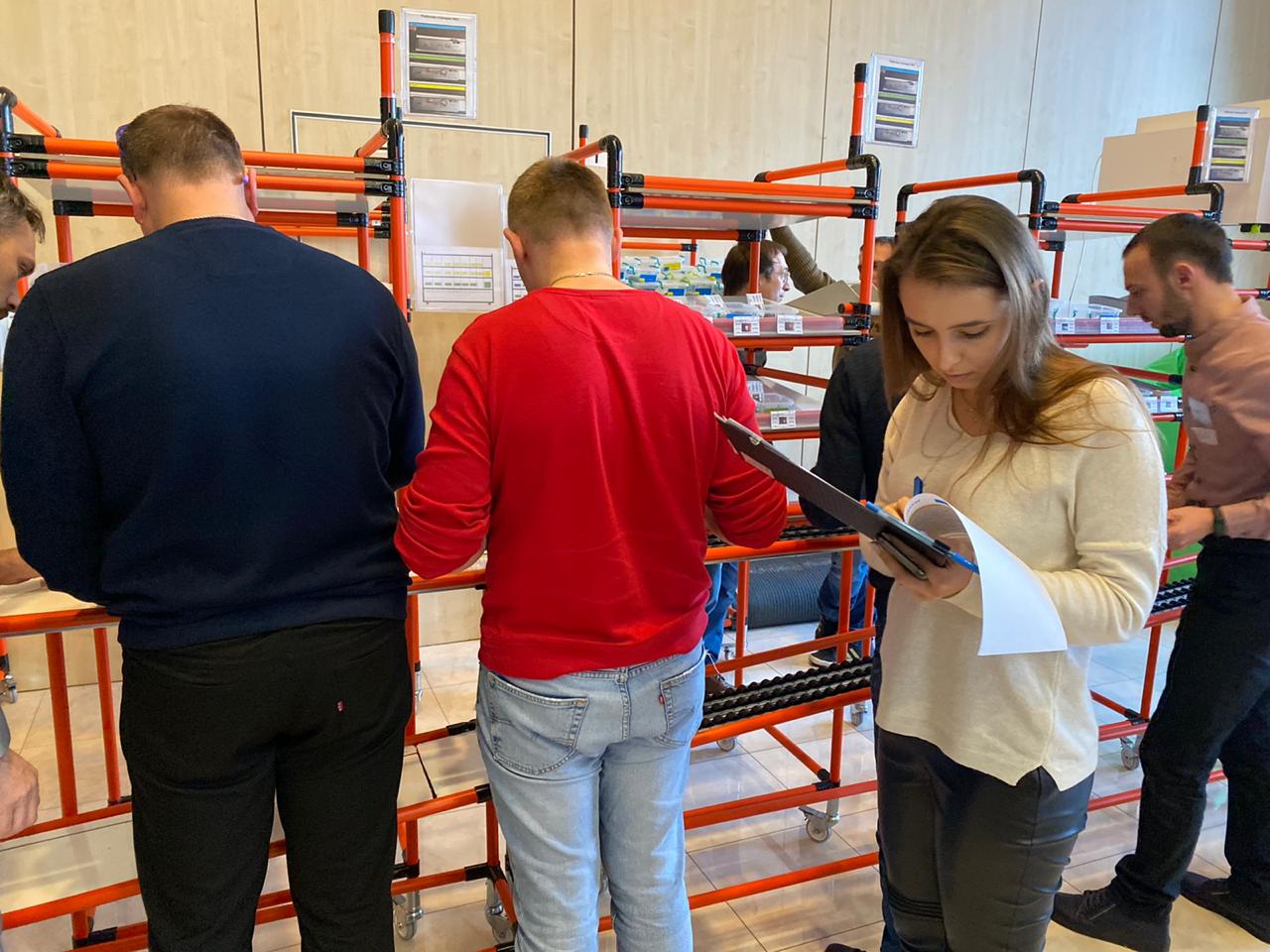
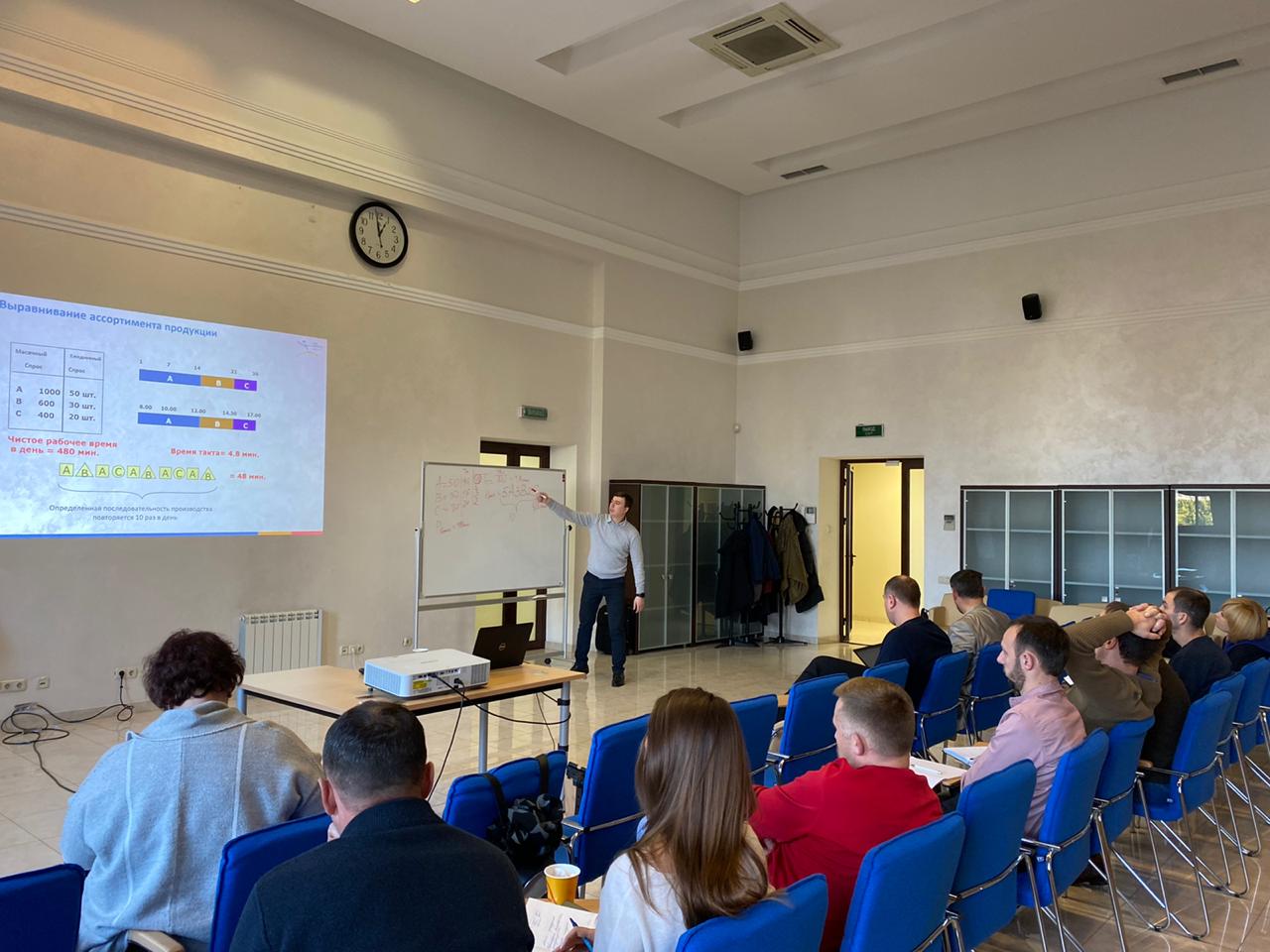